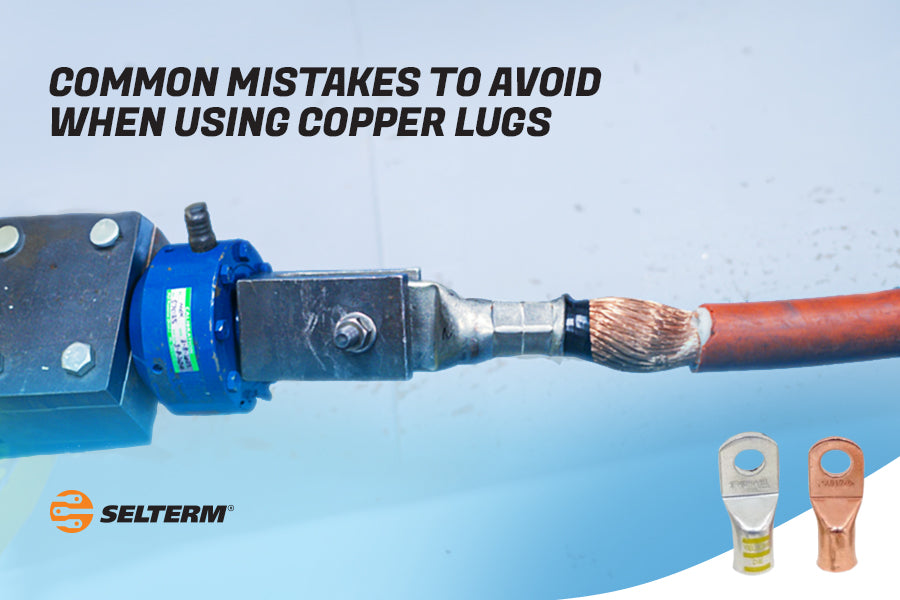
Common Mistakes to Avoid When Using Copper Lugs
Copper wire lugs are widely used in electrical systems for creating reliable and durable connections. Whether in industrial machinery, automotive wiring, or residential electrical systems, they ensure efficient conductivity and stability. However, improper use of copper lugs can lead to serious issues, ranging from equipment malfunction to safety hazards. Understanding the common mistakes associated with their usage can help professionals and DIY enthusiasts alike avoid costly and dangerous errors.
1. Choosing the Wrong Size Lug
One of the most common mistakes when using copper wire lugs is selecting the wrong size. Copper lugs come in various sizes to accommodate different cable diameters and amperage requirements. Using a lug that is too large or too small can compromise the connection:
-
Undersized lugs: These may not fit the cable properly, resulting in poor electrical contact and increased resistance.
-
Oversized lugs: These can cause loose connections, which may lead to overheating and potential equipment failure.
To avoid this mistake, always verify the cable’s cross-sectional area and the lug’s specifications to ensure compatibility.
2. Neglecting Proper Crimping Techniques
Crimping is a critical step in the installation of copper lugs. Incorrect crimping can result in a weak or unreliable connection. Common crimping mistakes include:
-
Using the wrong crimping tool: Each lug type requires a specific crimping tool designed to deliver the correct pressure and shape.
-
Insufficient crimping force: This can leave air gaps, increasing resistance and the risk of overheating.
-
Over-crimping: Excessive force can damage the lug or the conductor, compromising the connection.
Always follow the manufacturer’s guidelines for crimping tools and techniques to ensure a secure and durable connection.
3. Skipping Cable Preparation
Proper preparation of the cable before installing a copper lug is crucial. Neglecting this step can lead to poor connections and reduced performance. Common errors include:
-
Improper stripping of insulation: Stripping too much or too little insulation can expose bare wire or leave excess insulation inside the lug.
-
Failure to clean the conductor: Corrosion, dirt, or oxidation on the conductor surface can impede electrical conductivity.
Ensure the conductor is clean and stripped to the appropriate length to achieve optimal performance.
4. Ignoring Environmental Factors
Heavy duty lugs are often used in environments subject to varying temperatures, moisture, or corrosive elements. Failure to consider these environmental factors can lead to premature wear and failure. Common mistakes include:
-
Using standard lugs in harsh environments: Standard copper lugs may not withstand extreme conditions, leading to corrosion and reduced lifespan.
-
Neglecting protective measures: Lack of insulation, heat shrink tubing, or protective coatings can expose the connection to environmental damage.
For installations in challenging conditions, use tinned heavy duty lugs or apply protective measures to enhance durability.
5. Overlooking Torque Specifications
Proper tightening of bolts or screws is critical when securing copper lugs to terminals. Over-tightening or under-tightening can both lead to problems:
-
Over-tightening: This can deform the lug or damage the conductor, reducing the integrity of the connection.
-
Under-tightening: Loose connections can cause arcing, overheating, and eventual failure.
Always use a torque wrench and adhere to the manufacturer’s recommended torque values for secure and reliable connections.
6. Reusing Damaged or Old Lugs
Reusing old or damaged copper lugs is a common cost-saving practice that can backfire. Over time, lugs can suffer from wear, deformation, or corrosion, making them less effective. Reinstalling such lugs increases the risk of poor connections and system failures.
Always inspect wire lugs for signs of damage or wear and replace them as needed to maintain system reliability.
7. Failing to Test Connections
Skipping the testing phase after installing copper lugs is a critical oversight. Faulty connections may not be immediately apparent but can cause issues over time. Commonly overlooked tests include:
-
Resistance testing: Ensures the connection is conducting electricity efficiently.
-
Pull tests: Verifies that the lug is securely attached to the conductor.
-
Thermal testing: Identifies overheating issues under load conditions.
Incorporating these tests into your installation process can catch potential issues early and prevent future problems.
8. Using Incompatible Materials
Wire lugs should be used with compatible conductors and terminals to avoid galvanic corrosion. Pairing copper lugs with aluminum conductors, for instance, can lead to accelerated corrosion at the contact point.
If mixed materials must be used, apply a suitable joint compound to minimize the risk of corrosion and ensure a stable connection.
9. Inadequate Documentation and Labeling
Failure to document and label connections properly can create confusion during maintenance or troubleshooting. Misidentification of cables or connections can lead to errors and prolonged downtime.
Maintain clear and accurate documentation of all connections and label cables and lugs for easy identification.
Conclusion
Copper lugs are essential components for reliable electrical connections, but their effectiveness depends on proper selection, installation, and maintenance. By avoiding these common mistakes—choosing the wrong size, improper crimping, neglecting cable preparation, and more—you can ensure the longevity and performance of your electrical systems. Always adhere to best practices and manufacturer guidelines to achieve safe and efficient installations.