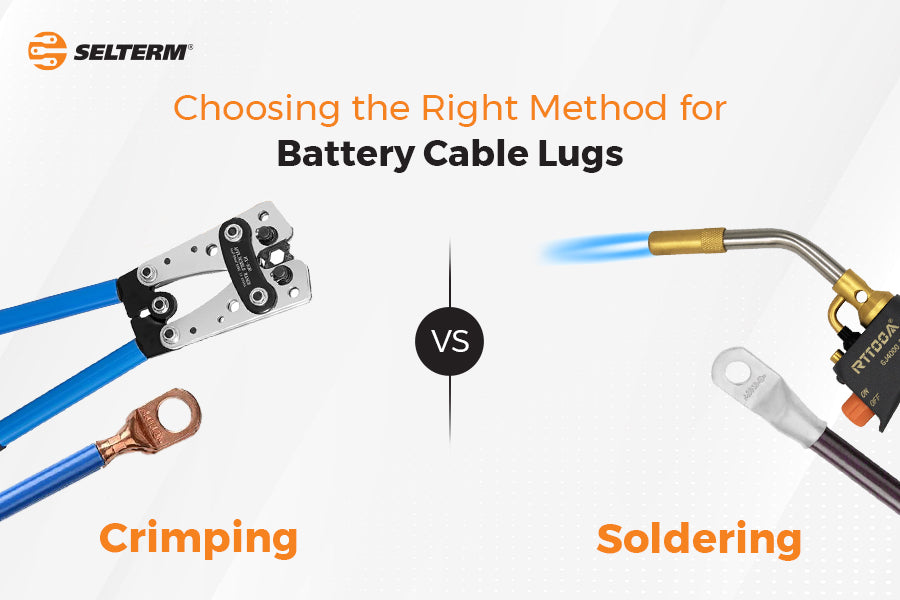
Crimping vs. Soldering: Choosing the Right Method for Battery Cable Lugs
Introduction:
When it comes to connecting battery cables, choosing the right method is crucial for ensuring a secure and reliable electrical connection. Two popular methods for attaching battery cable lugs are crimping and soldering. In this blog post, we'll explore the advantages and disadvantages of each method to help you make an informed decision for your specific application.
Crimping:
Crimping involves compressing a metal sleeve around the cable and soldering lugs using a specialized crimping tool. This method is widely used for its speed and ease of use. Here are some key points to consider:
- Efficiency and Speed: Crimping is generally faster than soldering, making it an attractive option for those looking to save time during installations or repairs.
- No Heat Required: Unlike soldering, crimping does not require heat. This eliminates the risk of damaging nearby components or causing thermal stress to the cable insulation.
- Consistent Results: When done correctly with the appropriate tools, crimping provides consistent results. Modern crimping tools are designed to exert precise pressure, ensuring a reliable connection every time.
- Accessibility: Crimping tools are readily available and come in various sizes, accommodating different cable and soldering lugs sizes.
Soldering:
Soldering involves melting a metal alloy (solder) to create a bond between the cable and the tinned copper lugs. While it requires more skill and time, soldering offers some unique advantages:
- Strength and Durability: Soldered connections tend to be more robust and durable over time, particularly in environments with vibrations or movement.
- Enhanced Electrical Conductivity: Soldering can improve the electrical conductivity of the connection, potentially leading to better performance in high-demand applications.
- Customization: Soldering allows for a more customized and aesthetically pleasing finish. This can be essential for applications where appearance matters.
- Higher Temperature Resistance: Soldered connections may have better resistance to high temperatures, making them suitable for applications in hot environments.
Choosing the Right Method:
The decision between crimping and soldering ultimately depends on your specific requirements and preferences. Consider the following factors:
- Application: For quick and efficient installations, crimping is often preferred. If durability and enhanced conductivity are critical, soldering may be the better choice.
- Skill Level: Crimping is generally more straightforward and requires less skill than soldering. If you're a novice or need a quick solution, crimping might be the better option.
- Tools and Equipment: Assess the availability of tools and equipment. Crimping tools are more common and may be more accessible than soldering equipment.
Conclusion:
Both crimping and soldering are valid methods for attaching Tinned copper lugs, each with its own set of advantages and disadvantages. SELTERM battery cable lugs are designed to work with crimping as well as soldering. Carefully assess your specific needs and priorities to determine which method is the best fit for your application. Whether you opt for the efficiency of crimping or the durability of soldering, a secure and reliable connection is crucial for the performance and safety of your electrical system.