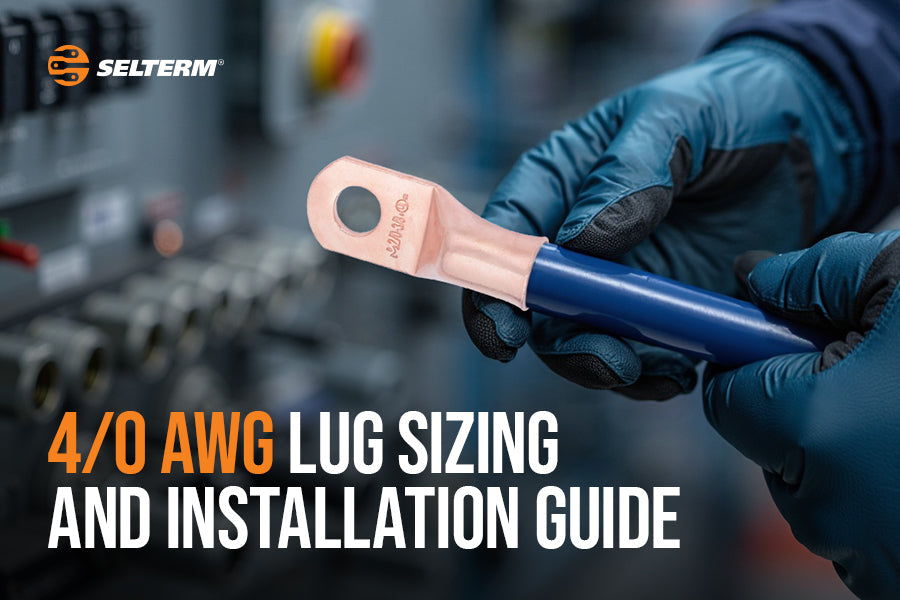
4/0 AWG Lug Sizing and Installation Guide: Ensuring Safe and Efficient High-Current Connections
In high-current applications, the choice of connectors is critical for ensuring safety and efficiency. 4/0 lugs are specifically designed to handle extremely large electrical loads, making them essential in industries such as power distribution, heavy-duty machinery, and large-scale off-grid systems. This guide provides a detailed overview of 4/0 awg cable lug sizing and installation best practices.
Understanding 4/0 AWG Lugs
4/0 lugs, also referred to as 4/0 battery terminals or 4/0 crimp lugs, are designed to terminate 4/0 AWG cables. This cable size is used in applications with very high current demands, where minimizing voltage drop and heat generation is crucial. The robust construction of 4/0 lugs ensures a reliable and secure connection under these demanding conditions.
Why Proper Sizing and Installation of 4/0 AWG Lugs Matter
- Safety: In high-current systems, improper connections can lead to overheating, arcing, and even electrical fires. Correct sizing and installation of 4/0 lugs are paramount to minimizing these risks.
- Efficiency: A well-executed connection minimizes resistance, ensuring efficient power transfer and reducing energy loss. This is crucial in high-load applications where even small inefficiencies can result in significant energy waste.
- Reliability: High-current systems often operate under continuous load and harsh conditions. Properly installed 4/0 AWG cable lugs provide a reliable connection that can withstand these stresses, reducing the risk of failures and downtime.
- Performance: Correctly sized and installed lugs ensure that the electrical system operates at its optimal performance, maintaining voltage stability and preventing equipment malfunctions.
Sizing Guidelines for 4/0 AWG Lugs
- Cable Diameter: The most critical factor in sizing 4/0 lugs is the diameter of the cable. The lug's barrel must match the cable's diameter precisely to ensure a secure and effective crimp.
- Stud Size: The stud hole in the 4/0 battery terminal must match the size of the terminal post or bolt to which it will be connected.
- Current Rating: Ensure that the lug is rated to handle the maximum current expected in the system. This information is typically provided by the manufacturer.
- Material Compatibility: Verify that the lug material is compatible with the cable conductor material to prevent galvanic corrosion.
Installation Best Practices for 4/0 AWG Lugs
- Cable Preparation: Strip the insulation from the cable to the correct length. For 4/0 lugs, the recommended strip length is approximately 1 inch or 25–32 mm. Ensure that the cable strands are clean and undamaged.
- Lug Selection: Choose a 4/0 crimp lug that matches the cable diameter and stud size. Use a high-quality lug that meets industry standards.
- Crimping: Use a hydraulic crimper specifically rated for 4/0 AWG cable lugs. Apply firm, even pressure to create a secure and gas-tight crimp.
- Inspection: After crimping, inspect the connection to ensure it is properly compressed and free from any loose strands. Perform a pull test to verify the mechanical strength of the connection.
- Secure Fastening: When connecting the lug to a terminal, use the correct hardware and torque settings. Follow the manufacturer's recommendations to avoid over- or under-tightening.
- Protection: Consider using heat shrink tubing to insulate the connection and protect it from moisture and corrosion.
Maintenance
- Regularly inspect 4/0 battery terminals and connections for any signs of wear, overheating, or corrosion.
- Tighten any loose connections and clean off any corrosion as needed.
Technical Details Recap
- Cable Gauge: 4/0 AWG
- Strip Length: Approximately 1 inch (25–32 mm)
- Recommended Tool: Hydraulic crimper rated for 4/0 AWG
- Ampacity: Typically 300–400A (depending on insulation and code)
Conclusion
Proper sizing and installation of 4/0 AWG lugs are crucial for ensuring the safety, efficiency, and reliability of high-current electrical systems. By following these guidelines and adhering to best practices, professionals can minimize the risk of electrical hazards and optimize the performance of their systems.