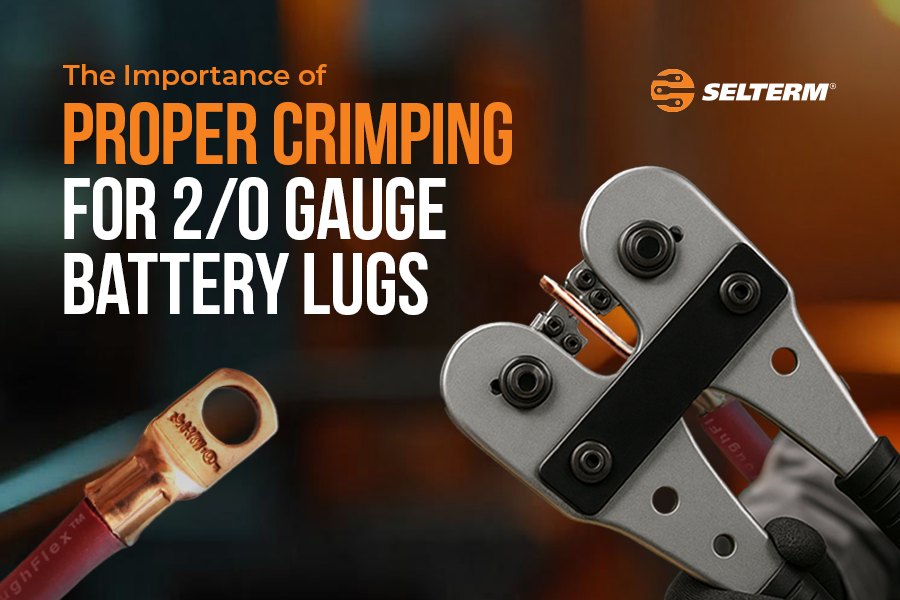
The Importance of Proper Crimping for 2/0 Gauge Battery Lugs
In the realm of high-current electrical systems, where the demand for power is substantial and the consequences of failure can be severe, the integrity of every connection is paramount. Battery connections, in particular, play a critical role, serving as the lifeline for starting engines, powering equipment, and supporting essential operations. 2/0 gauge battery lugs are frequently employed in these demanding scenarios due to their ability to handle significant electrical loads. However, the effectiveness and safety of these connections hinge on one crucial factor: proper crimping. This guide delves into the paramount importance of proper crimping for 2/0 gauge battery lugs, exploring its impact on electrical conductivity, safety, and overall system reliability.
Understanding 2/0 Gauge Battery Lugs
Before delving into the intricacies of crimping, it's essential to establish a clear understanding of 2/0 gauge battery lugs. The "AWG" designation, standing for American Wire Gauge, is a standardized system for measuring wire diameter. 2/0 AWG represents a large wire size, indicating its capacity to carry very high currents. 2/0 AWG battery lugs are specifically designed to terminate these large-gauge cables, providing a secure and efficient connection point to the battery terminal. These lugs are typically constructed from high-conductivity copper, a material chosen for its ability to minimize resistance and ensure the smooth flow of electricity. The robust design of 2/0 gauge battery lugs is essential for withstanding the mechanical stresses and thermal demands of high-current applications.
The Crucial Role of Crimping
Crimping is the process of joining a lug to a wire or cable by compressing the lug barrel tightly around the conductor. This process is the most common and, when done correctly, the most effective method for creating a reliable electrical connection. In the context of 2/0 gauge battery lugs, where high currents are involved, the importance of proper crimping cannot be overstated.
- Electrical Conductivity: The primary function of any electrical connection is to provide a low-resistance path for current to flow. A properly executed crimp creates a gas-tight seal between the lug and the wire, maximizing the contact area and minimizing resistance. This ensures efficient power transfer and prevents energy loss in the form of heat. In contrast, an improperly crimped connection introduces resistance, impeding current flow and causing the connection to heat up. This heat can damage the wire insulation, the lug, and even the battery terminal, potentially leading to system failure.
- Safety: Safety is paramount in high-current electrical systems. A loose or poorly crimped connection poses a significant safety hazard. The increased resistance at the connection point generates heat, which can ignite surrounding materials, causing a fire. Additionally, loose connections can lead to arcing, the flow of electricity through the air between two conductors. Arcing can damage equipment and also poses a fire risk. Proper crimping eliminates these risks by creating a secure and stable connection that can handle the high currents without overheating or arcing.
- Reliability: The reliability of a battery system is directly linked to the dependability of its connections. A properly crimped 00 gauge lugs provides a robust and long-lasting connection that can withstand vibration, mechanical stress, and temperature fluctuations. This ensures consistent performance and minimizes the risk of connection failures, which can lead to equipment malfunction, downtime, and costly repairs.
Best Practices for Crimping 2/0 Gauge Battery Lugs
Achieving a proper crimp on 2/0 gauge battery lugs requires careful attention to detail and adherence to best practices:
1. Cable Preparation: The first step is to prepare the cable correctly.
- Stripping: Carefully strip the insulation from the end of the cable to the appropriate length. The ideal strip length typically corresponds to the barrel length of the lug, ensuring that the entire conductor is in contact with the lug. Precision is crucial here. Stripping too much insulation exposes excessive wire, increasing the risk of shorts. Stripping too little insulation results in insufficient contact, leading to increased resistance. Use a wire stripper tool to avoid nicking or cutting any of the strands, as damaged strands reduce the cable's current-carrying capacity.
- Cleaning: Ensure that the exposed cable strands are clean and free of any dirt, grease, or corrosion. Contaminants can impede conductivity and compromise the integrity of the connection. If necessary, use a wire brush or cleaning solution to remove any debris before proceeding.
2. Lug Selection: Choosing the right lug is essential.
- Size: Select a lug that is precisely matched to the cable size. Using an undersized lug will restrict current flow and create a point of excessive heat. An oversized lug may not provide a secure crimp.
- Quality: Opt for high-quality 2/0 wire lugs from a reputable manufacturer. The lug should be constructed from high-conductivity copper and have a uniform tin coating if corrosion resistance is required. Avoid using damaged or corroded lugs.
3. Crimping Tool: The crimping tool is just as important as the lug itself.
- Type: Use a crimping tool specifically designed for the lug size. Hydraulic crimpers are often preferred for larger battery copper lugs, as they provide the necessary force for a secure and gas-tight crimp. Ensure that the tool is in good working condition and properly calibrated.
- Technique: Position the lug and cable correctly in the crimping tool. Apply firm, even pressure until the crimp is complete. Follow the tool manufacturer's instructions for the specific crimping procedure. A proper crimp creates a metallurgical bond between the lug and the cable, ensuring optimal conductivity.
4. Inspection: After crimping, thoroughly inspect the connection.
- Compression: Visually verify that the lug is uniformly compressed around the cable. There should be no gaps or loose strands.
- Pull Test: Perform a gentle pull test to ensure the mechanical strength of the connection. The lug should not move or come loose.
5. Protection: Consider adding an extra layer of protection.
- Heat Shrink Tubing: Apply heat shrink tubing over the connection to provide insulation and environmental protection. This is particularly beneficial in harsh environments where moisture or chemicals are present.
Technical Details Recap
- Cable Size: 2/0 AWG
- Lug Material: Copper (Tinned Copper for corrosion resistance)
- Crimping Tool: Hydraulic Crimper (Recommended)
Proper crimping is not merely a procedural step; it is the cornerstone of a safe, reliable, and efficient high-current electrical system. By adhering to best practices and paying meticulous attention to detail, professionals and enthusiasts can ensure that their 00 gauge batter lugs connections provide years of dependable service.